
SINCE 1985
CAN GROUP OF COMPANIES
CAN Textile is an integrated woven fabric producer. Our company was established in 1985, initially producing 350 tons of yarn per month. Over the years, we have expanded significantly, becoming an integrated fabric producer. Key milestones include the establishment of our weaving mill in 1989, the dyeing and finishing mill, along with a wastewater treatment system, in 1993, and the co-generation department in 1996.
- 1985 Spinning Mill
- 1989 Weaving Mill
- 1993 Dyeing and Finishing Mill + Wastewater Treatment Plant
- 1995 ISO 9001 QMS , ISO 14000 EMS(first in sector)
- 1996 Oeko-Tex
- 1997 Export Operations started
- 1998 AQAP 110 Nato
- 2004 Can Enerji Entegre Elektrik Üretim A.Ş.
- 2004 LifeMed – Health Clinique
- 2004 ISO 45001 Occ.Health and Safety Man.Sys.
- 2007 Green House 1. Plant
- 2007 Can Enerji Wholesales
- 2008 GLOBAL-GAP (first in sector)
- 2008 Medicheck Parmacy Products
- 2009 Green House 2. Plant
- 2009 Trakya University Healty Center
- 2010 Can Enerji in Tekirdağ Naturalgas
- 2012 Can Enerji-Trabzon HES , Bilecik Metris-tepe RES
- 2015 ISO 50001 Energy MS
- 2016 Sustainability Higg Reporting
- 2017 Can R&D Center
- 2019 Global Recycled Standard (GRS)
- 2019 ISO 28000 Supply Chain Security Management System
- 2019 Home textile & outdoor fabric production
- 2020 Organic Content Standard (OCS) , Sewing Plant
- 2021 Greenhouse Investment (indoor and outdoor plants)
- 2022 ISO/IEC 27001 , ISO 14064 , Authorised Economic Operator
- 2023 BOUN - ÇŞİDB National Project , Forest Steward Council
- 2024 Recycled Content Standard (RCS)Responsible Wool Standard (RWS)

1,000,000 meters OF FABRICS per month
The average total fabric production capacity is 1,000,000 meters per month. CAN Textile, with 70% of its production exported, is located in Çorlu, Tekirdağ. The facility spans 400,000 m², with 110,000 m² of built interior space, and employs nearly 1,200 people under one roof. At these facilities, yarn is spun using state-of-the-art ring spinning technology, and fabric is woven on rapier and air-jet looms, allowing for a wide variety of designs. The dyeing and finishing plant, equipped with the latest technology, produces both piece-dyed and yarn-dyed fabrics.
WEAVING MILL
The weaving mill, which has started its production in 1989, is equipped with rapier and air jet looms and these has capacity to weave men’s & women’s outerwear fabrics in different compositions such as: Polyester, Polyamide, VISCOSE, Polyester / Viskon, Tencel, Lycra / Polyester / VISCOSE, Melange, Mechanical strech, Tencel / Linen, Viscose / Linen, Polyester / Viscose / Linen, Tencel / Polyester, Polyamide / Viscose
DYEING & FINISHING MILL
In the dyeing & finishing mill, which has been added to production in 1993, piece dyeing and yarn dyeing can be done with HT type machines. The fabric gets its last shape, handle and appearance before it is sent to the customers.
LABORATORIES
• YARN TESTING LABORATORY
• DYE LABORATORY
• FABRIC TESTING LABORATORY
• WASTE WATER TREATMENT LABORATORY
QUALITY CONTROL
After weaving process, the greige fabric 100% controlled and all the defects are marked on computer, it is sent to for the dyeing & finishing process. All finished fabric is also 100% controlled by taking into consideration the customer demands and criteria’s.

Our company and fabric certificates
OEKO_TEX_21.HTR.82762
OEKO_TEX_97.T.1049
Scope Certificate USB TEX2581-MUL-2022-01
ISO9001_TR_2023
ISO14001_TR_2023
ISO50001_TR_2023
ISOIEC27001_TR_2023
SEDEX
SUSTAINABILITY_FSLM_vm certificate
SUSTAINABILITY_HIGG_FEM_vm certificate
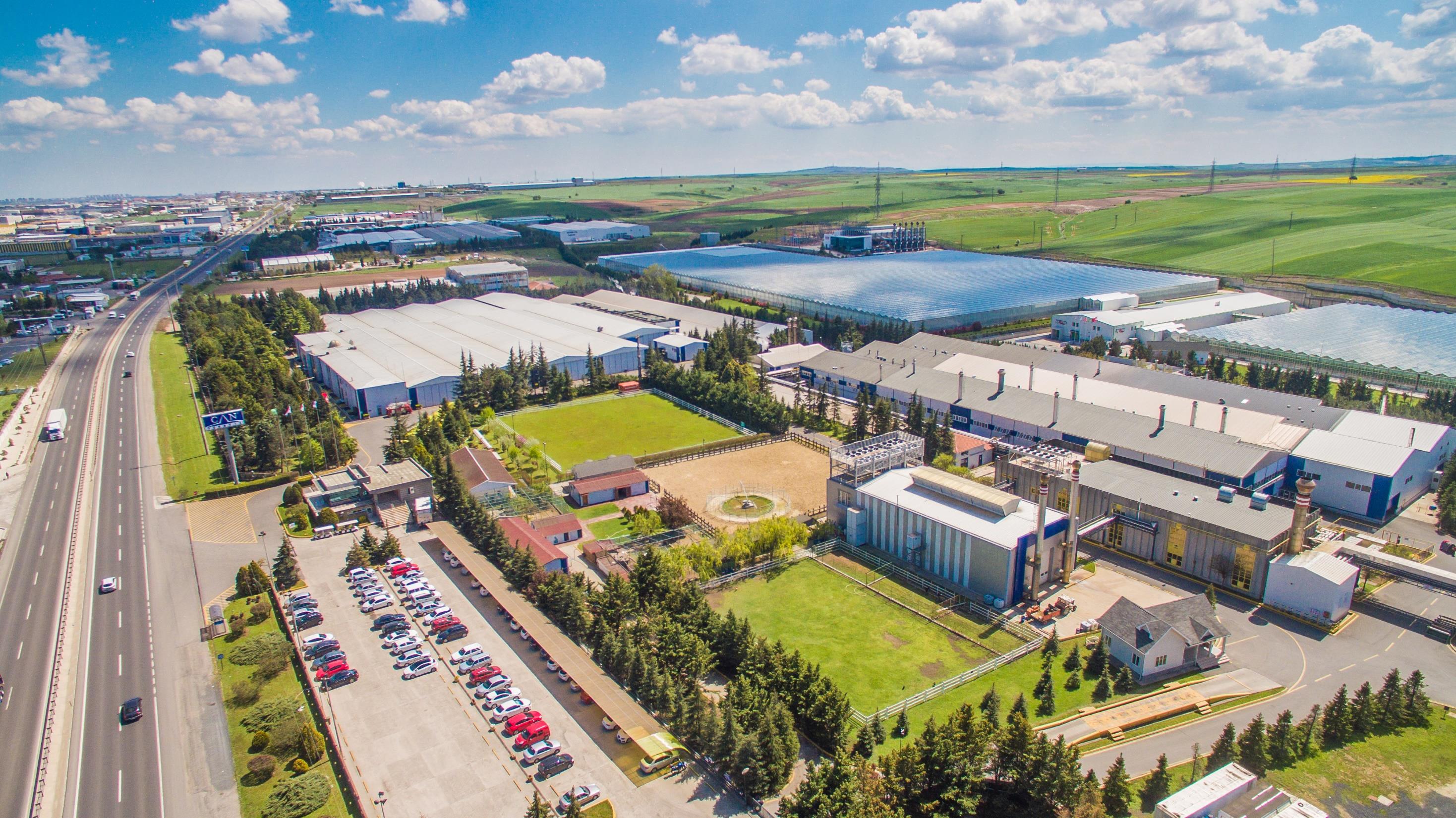
Video